Midtown Lofts
On this project, HCM in conjunction with RWH Engineering Inc. (RWH), provided the owner with a complete design-build package and precision monitoring services for an 8.5m deep temporary shoring system.
RWH produced a tailored piles and lagging shoring design. As tiebacks were not feasible on the project due to encroachment limitations, RWH provided a waler and raker design that minimized interference as construction progressed.
HCM worked closely with the general contractor during pile installation and lagging to ensure that excavation proceeded safely and on schedule. Precision monitoring was implemented and reviewed by RWH throughout the project to confirm the integrity of the shoring system and surrounding infrastructure.
Client: GUPM Construction Managers
Location: Kitchener, Ontario
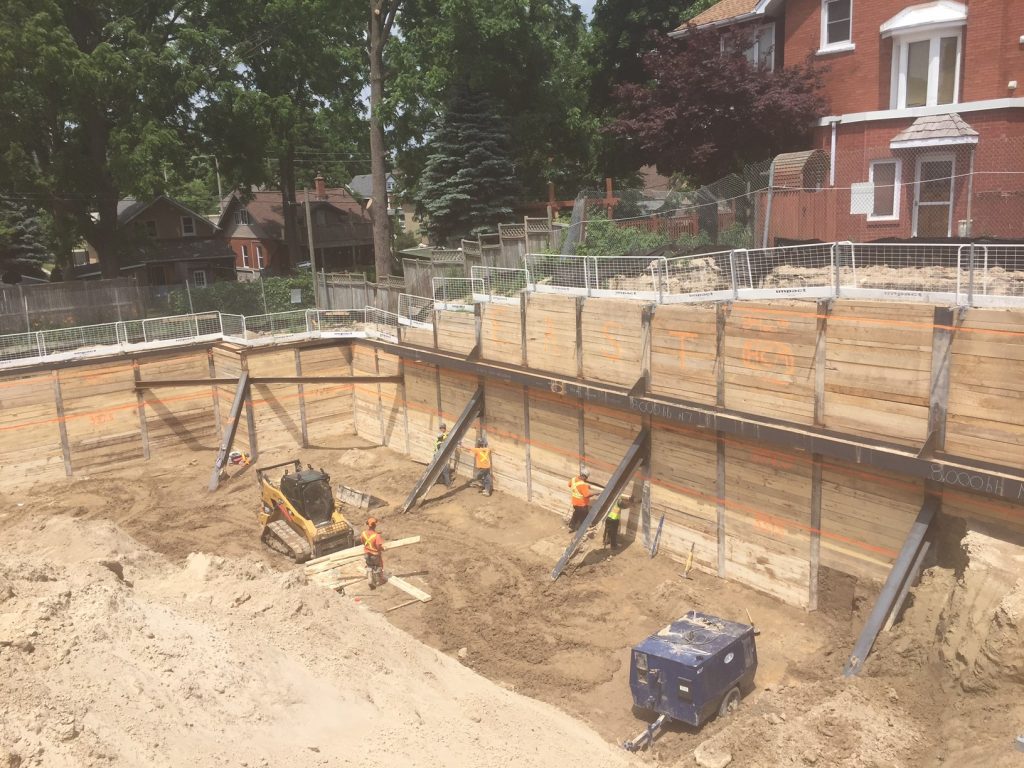