WHAT IS SHOTCRETE?
“Shotcrete” is a term that is used to describe concrete that is pneumatically projected at high velocity onto a surface.
Frequently Asked Questions
What is shotcrete?
Shotcrete is concrete that is pneumatically projected at high velocity onto a surface. Shotcrete is typically classified into two categories:
- Wet mix process: concrete is batched, delivered to site, and pumped to the shotcrete nozzle where compressed air is added to the flowing material just prior to shooting.
- Dry mix process: concrete ingredients excluding water are mixed and delivered to the shotcrete nozzle using compressed air. Water is added to the dry materials at the nozzle, just prior to shooting.
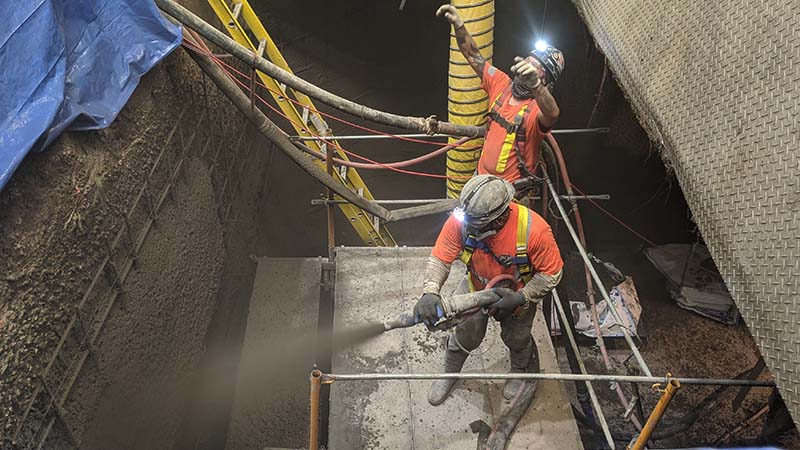

Shotcrete finishes:

Nozzle Finish
(typical of shoring applications)
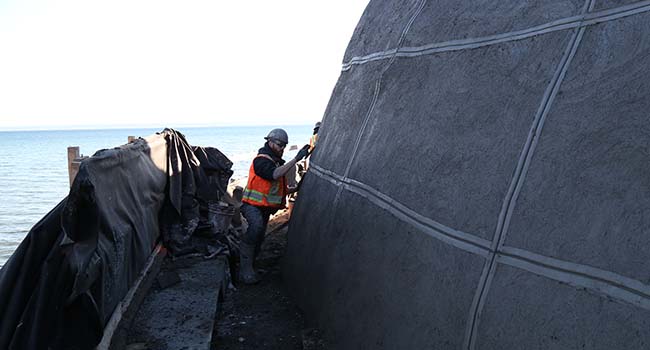
Architectural Finish
(textured as per request)

Smooth Steel Troweled Finish
(typical of structural shotcrete applications)
Are there any special design considerations for shotcrete?
Shotcreting is a method of placing concrete – when properly executed the final product is equivalent or superior to formed concrete. No special design considerations are required
– CSA 23.3 and 23.4 apply to shotcrete works.
Shotcrete mix designs can be proportioned to meet specified performance requirements including chloride, sulphate, and freeze/thaw resistance.
As with any type of concrete placement, qualified installers, material suppliers, and quality control practices are required to ensure the overall quality of the shotcrete.
What about rebar encapsulation?
In the shotcrete process, rebar encapsulation is achieved by utilizing impact force as a means of consolidation. Encapsulation is monitored closely by the project team throughout shotcreting operations. Trained (ACI certified) and experienced shotcrete nozzlemen apply a variety of techniques to ensure quality rebar encapsulation during shotcreting operations. The advantage of shotcrete over a formed wall construction is that the reinforcing steel is visible until it is encapsulated by shotcrete.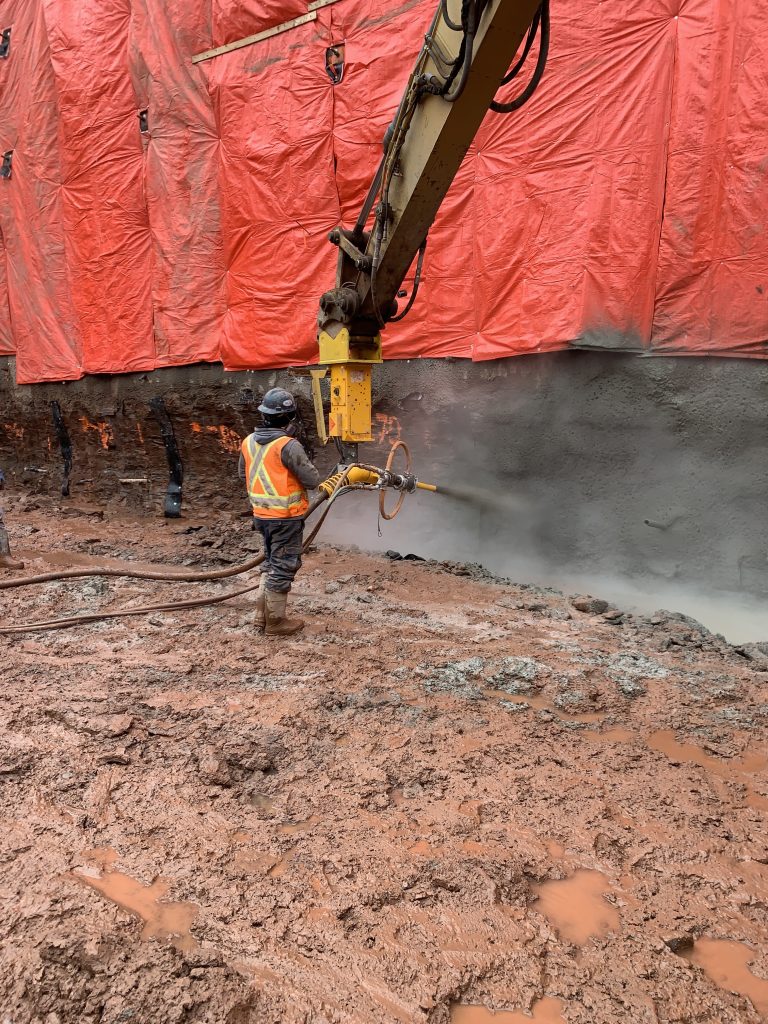
How does shotcrete compare to conventional formed wall construction with respect to shrinkage cracking?
- lower water to cement ratio than formed wall mixes;
- lower slump requirements;
- use of low water demand supplementary cementing materials (slag);
- use of supplementary wire mesh reinforcement;
- use of fiber reinforcement to control shrinkage;
- use of shrinkage control admixtures;
- prudent curing.
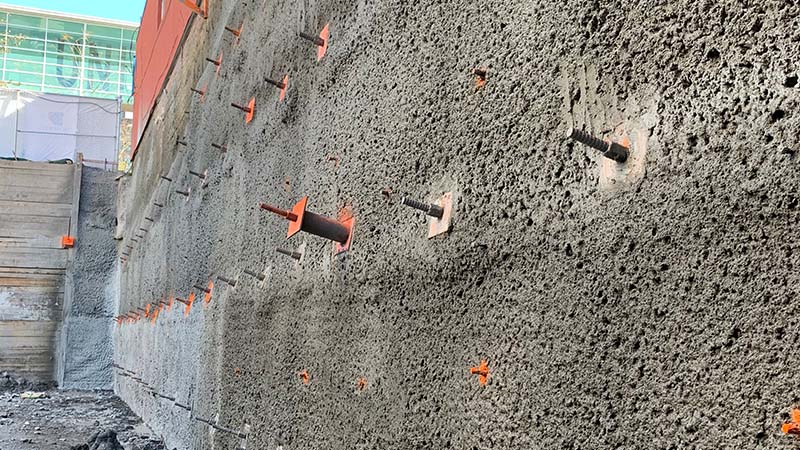
What are curing requirements for shotcrete?
Shotcrete should be cured in the same way as any type of exposed concrete. Formed walls are typically not wet cured as they have formwork in place to guard against excessive water loss. Shotcrete can be cured in any or a combination of the following ways:
- continuous misting – best practice;
- wet medium (i.e burlap) – good practice
- curing compound – acceptable method, typically applied at twice the manufacturers recommended application rate.
What are the similarities/differences between a structural shotcrete mix design and a typical formed wall mix design?
Compressive Strength: structural shotcrete is designed to meet or exceed specified compressive strength requirements.
Are control joints required?
Without control joints, shrinkage cracking will not be contained within a set pattern and detailed to control water leakage. In shotcrete applications, because the face of the wall is accessible, it is possible to introduce regular control joints (tooled or cut) to contain shrinkage cracking.
How are cold joints treated?
Cold joints in shotcrete walls are similar to cold joints in formed walls. Depending on the designer’s requirements, a key may be required at cold joint locations. Similar to formed walls, exposed reinforcing steel that is not being cast in concrete must be kept clean or cleaned following concrete placement.
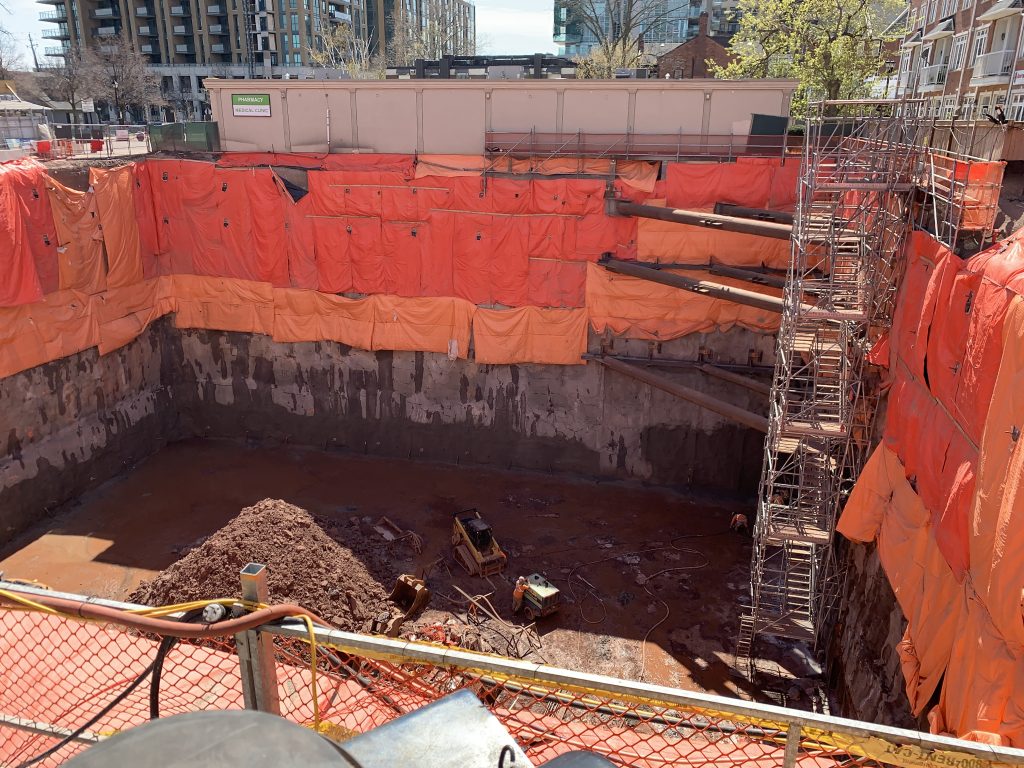
What are precautions for cold weather and hot weather shotcreting?
Cold Weather: typical precautions including adjustment of mix to reflect cold weather
(warm mix water, non-chloride accelerator) and protection of work area. Similar to formed wall construction, the fresh shotcrete needs to be insulated or heated to protect against freezing and to maintain temperatures required for design strength gain. In the absence of formwork to secure insulation to, heated enclosures or draped insulating blankets are used.
Hot Weather: typical precautions including adjustment of mix to reflect hot weather (cold mix water, ice, set retarder) and protection of work area from direct sunlight. In addition to these precautions, curing may need to begin immediately following placement (if finishing is not immediately possible) and continued immediately following finishing. Evaporation reducers may be used to minimize surface evaporation prior to finishing. Micro fibers can also be added to reduce plastic shrinkage cracking in severe environments.
References:
“ACI 209.1R-05 – Report on Factors Affecting Shrinkage and Creep of Hardened Concrete” ACI Manual of Concrete Practice. Comp. American Concrete Institute. 2012 ed. Vol. 6. Farmington Hills, MI: American Concrete Institute, 2012.
“ACI 306R-10 – Guide to Cold Weather Concreting” ACI Manual of Concrete Practice. Comp. American Concrete Institute. 2012 ed. Vol. 6. Farmington Hills, MI: American Concrete Institute, 2012.
“ACI 308R-01 – Guide to Curing Concrete” ACI Manual of Concrete Practice. Comp. American Concrete Institute. 2012 ed. Vol. 6. Farmington Hills, MI: American Concrete Institute, 2012.
“ACI 506R-05 – Guide to Shotcrete” ACI Manual of Concrete Practice. Comp. American Concrete Institute. 2012 ed. Vol. 6. Farmington Hills, MI: American Concrete Institute, 2012.
Morgan, D. R. “Understanding and Controlling Shrinkage and Cracking in Shotcrete.”Shotcrete: A Compilation of Papers. Farmington Hills, MI: American Shotcrete Association, 2008.