McMaster Nuclear Building
The nuclear research building was an upgrade to the existing structure to allow for world class nuclear research for leading nuclear scientists. This project was funded by the provincial and federal governments as part of a stimulus package for Hamilton, Ontario. This project required a deep foundation solution to support the proposed structure next to the existing nuclear building.
Helicals were designed and installed with 4.5” diameter helical pipe to allow for desired corrosion protection. Load testing confirmed the ULS loading and the design was based on a SLS of 400KN. RWH, an HC Group company, worked very closely with the structural engineer, Atkinson, to ensure SLS settlements and differentials were less than the specified 1/2” maximum. The helicals were founded 30ft deep in a layer that provided sufficient resistance but required very accurate placement due to wet, poor soils located just above and below the layer. An important challenge to note was that construction and excavation was performed beside the nuclear testing building and vibrations had to be kept to a minimum due to sensitive equipment located inside.
HC Matcon’s operators and site supervisors performed their work with a very high degree of skill allowing successful installation of the helicals while proceeding on schedule with the contract timeline. HC Matcon also provided zero clearance shotcrete complete with excavation in a second stage contract, working with a new owner, to attain budgeted costs allowing that contract to proceed with government grants. This is also an excellent example of the HCM/RWH service in design build of helical piers.
Client: IRA MCdonald Construction Limited
Location: Hamilton, Ontario
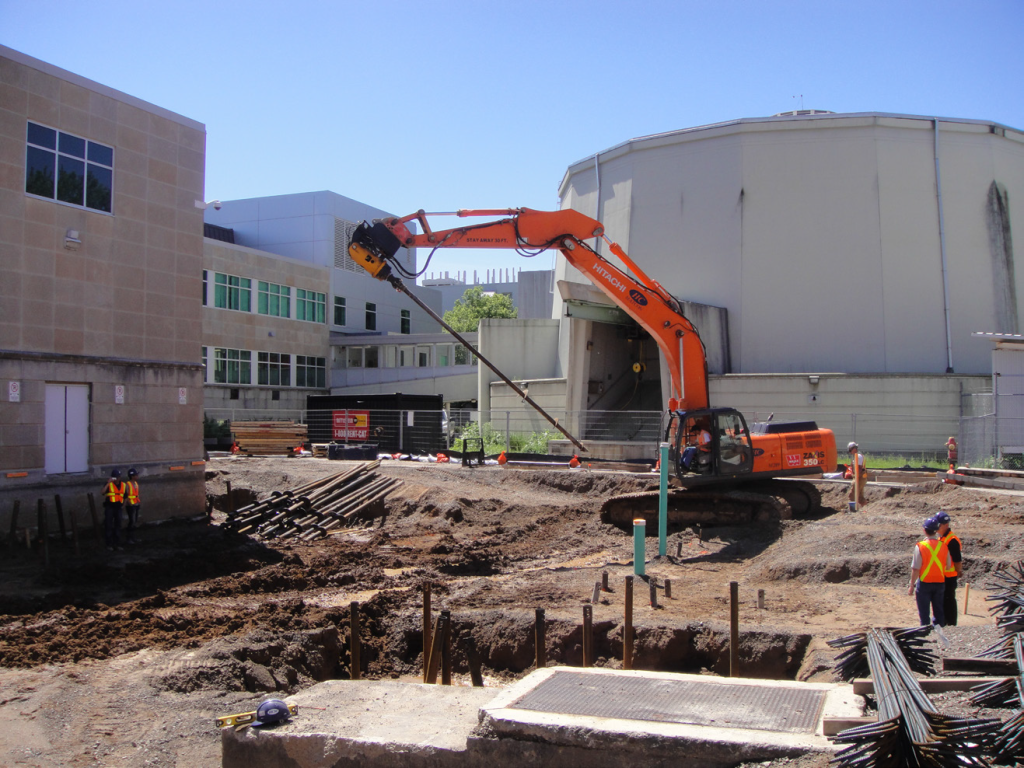
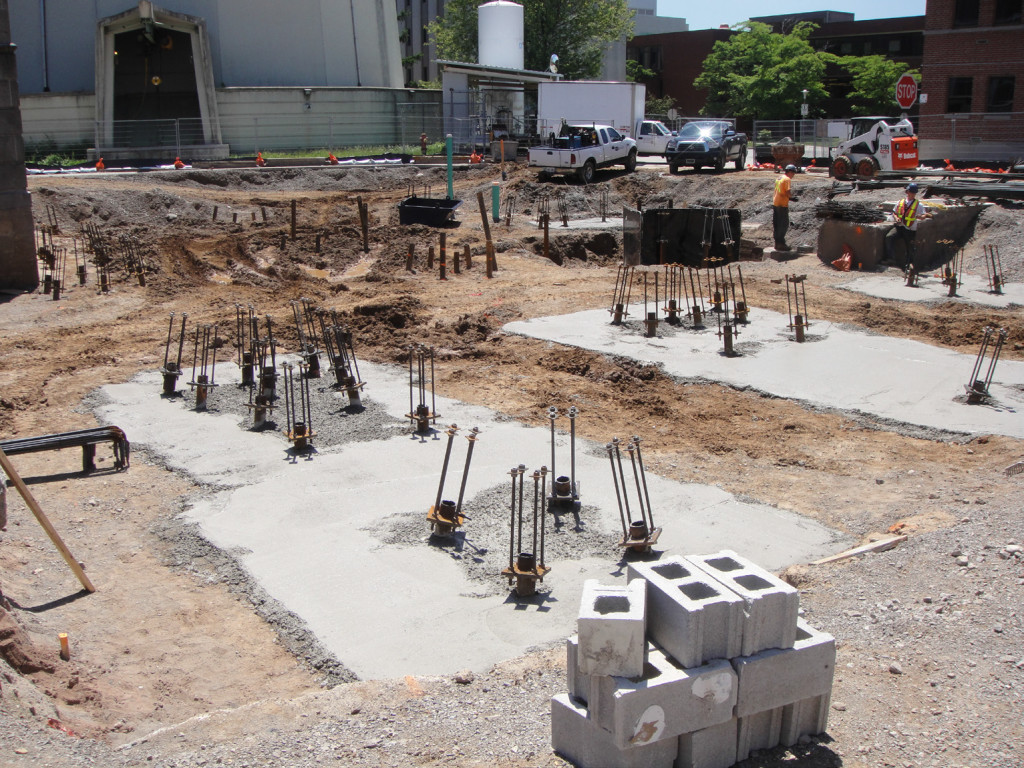